Die Digitalisierung der Produktion ist kein Luxus mehr, sondern eine Notwendigkeit. Doch gerade...
Produktion unter Druck – welche Investitionen lohnen sich im Spritzguss wirklich?
Immer wieder stoße ich bei Gesprächen mit Spritzgießunternehmen auf ein ähnliches Bild: Die zugrunde liegenden Kalkulationen stammen oft noch aus Zeiten, in denen Energiepreise und Rohstoffkosten deutlich niedriger waren – mitunter zehn Jahre alt. Klar, manche Grundlagen ändern sich nie. Aber die Welt drumherum hat sich dramatisch verändert.
Seit 2020 hat sich unsere Realität gewaltig verschoben: Pandemie, Lieferkettenkrisen, geopolitische Spannungen, Inflation und eine spürbare Klimaveränderung. Diese Faktoren beeinflussen heute massiv die Produktionskosten im Spritzguss.
Daher mein Appell an die Branche: Jetzt ist der ideale Zeitpunkt, um bestehende Kalkulationen zu aktualisieren und Investitionsentscheidungen neu zu bewerten.
Inhalt:
-
Welche Bereiche treiben aktuell die Kosten?
-
Welche Investitionen zahlen sich langfristig aus?
-
Fazit: Investieren trotz Krise?
Die Hauptkostentreiber im Spritzguss (2023–2024).png?width=83&height=46&name=Website%20Tests-7%20(2).png)
1. Energie und Stromkosten 2023 lag der durchschnittliche Industriestrompreis in Österreich bei etwa 20 ct/kWh (inkl. Abgaben und Netznutzung) – doppelt so hoch wie noch vor wenigen Jahren. Große Verbraucher wie Trockner oder Heizbänder in Spritzgussanlagen verursachen dadurch immense Kosten.
Praxisbeispiel: Bei einem COISS-Kunden verursachte allein der energieintensive Trockner einer Maschine jährliche Stromkosten von knapp 9.500 €. Früher lag der Wert bei etwa 3.800 €.
2. Prozessineffizienzen & ungeplante Stillstände Stehende Maschinen verbrauchen weiter Strom – insbesondere beim Halten von Betriebstemperaturen. Solche Stillstände bleiben oft unentdeckt oder werden zu spät behoben.
Beispiel aus 2024: Ein mittelständischer Betrieb zahlte im Jahr 2023 etwa 145.000 € für Strom. Nach Analyse mit COISS zeigte sich: 27 % davon entfielen auf beheizte Stillstände.
3. Rohstoffpreise & Materialverschwendung Der Preis für Polycarbonat lag 2023 bei etwa 6,80 €/kg, für ABS sogar bis zu 7,50 €/kg. Kurzstillstände oder Prozessabweichungen führen zu Ausschussmaterial, das teuer entsorgt wird.
COISS-Einblick: Kurzstillstand pro Tag = Materialverlust ≈ 12 €. Auf 30 Maschinen ergibt das über ein Jahr rund 131.400 € an unnötigen Kosten.
4. Personalengpässe & Ineffizienz im Shopfloor Der Fachkräftemangel führt dazu, dass Maschinen zu lange stillstehen, weil niemand da ist, um sofort zu reagieren. Besonders in "Geisterschichten" (z. B. Nachtbetrieb) ist das ein großes Thema.
COISS-Lösung: Durch Echtzeit-Benachrichtigungen per Tablet konnte ein Kunde seine Reaktionszeit auf Stillstände um 70 % senken und rund 4.600 Maschinenstunden pro Jahr zurückgewinnen – ohne Neueinstellungen.
5. Klimaziele & Gesetzesvorgaben Mit der Einführung von Regulierungen wie ESPR (Ecodesign-Verordnung) oder dem Digital Product Passport steigt der Druck auf Unternehmen, transparenter und klimabewusster zu produzieren. Auch das CSRD-Gesetz verpflichtet ab 2024 viele Unternehmen zur Nachhaltigkeitsberichterstattung.
Diese Investitionen zahlen sich trotzdem aus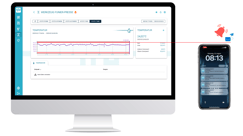
Gerade in wirtschaftlich fordernden Zeiten sind gezielte, skalierbare Investitionen der Schlüssel. Folgende Bereiche zeigen laut COISS-Datenlage besonders hohe Wirkung:
1. Digitale Energieüberwachung & -optimierung
Schon mit geringem Aufwand lassen sich "Stromfresser" identifizieren. COISS-Kunden setzen etwa auf Sensorik zur Analyse von Stillstandszeiten und Energieverbrauch.
Beispiel: Eine Investition von 11.000 € in COISS-Sensorik und Monitoring-Software sparte einem Kunden 48.000 € pro Jahr – ROI: 4,4.
2. Predictive Maintenance & Condition Monitoring
Prozesse stabilisieren, Wartungen vorausschauend planen und Ausfälle vermeiden: Mit COISS-Sensoren erkennen Betriebe kritische Zustände, bevor sie teuer werden.
3. Smarte Reaktionssysteme für den Shopfloor
Stillstände erkennen und in Echtzeit benachrichtigen – per Tablet, Smartphone oder Display. Das entlastet Personal und erhöht die Produktionseffizienz, ohne mehr Leute einstellen zu müssen.
4. Ressourceneinsparung bei Rohstoffen
COISS-Analysen zeigen: Bereits kleine Optimierungen bei Temperaturprofilen oder Dosierung sparen Granulat und Energie. Bei manchen Kunden konnte der Rohstoffverbrauch um bis zu 7 % gesenkt werden.
Fazit: Investieren in unsicheren Zeiten?
Ja. Vorausgesetzt, es sind die richtigen Hebel. Unsere Erfahrung bei COISS zeigt, dass Investitionen in Transparenz, digitale Prozesse und Effizienz auch in der Krise stark wirken. Sie reduzieren laufende Kosten, verbessern die Produktionsleistung und unterstützen gleichzeitig beim Erreichen gesetzlicher Vorgaben.
Und das Beste: Die meisten Projekte rechnen sich bereits im ersten Jahr.
Wer jetzt vorbereitet ist, hat 2025 einen entscheidenden Vorsprung.