Die digitale Transformation verändert die Fertigungsindustrie grundlegend. Während viele...
Motorlager zerfetzt! Frühzeitige Erkennung von Ausfällen durch Anomalieerkennung und Vibrationsüberwachung
Frühzeitige Erkennung von Ausfällen und Motorschäden durch Anomalieerkennung und Vibrationsüberwachung
Industrieunternehmen stehen vor der Herausforderung, ungeplante Maschinenstillstände zu minimieren und teure Reparaturen zu vermeiden. Eine effektive Lösung bietet die Kombination aus Anomalieerkennung und Vibrationsüberwachung. Diese Technologien helfen, Motorlagerschäden frühzeitig zu identifizieren, Ausfälle zu verhindern und erhebliche Kosten zu sparen. Laut einer Studie von McKinsey & Company kann Predictive Maintenance die Wartungskosten um bis zu 40 % senken und ungeplante Stillstandszeiten um bis zu 50 % reduzieren.
Wie funktioniert die Anomalieerkennung?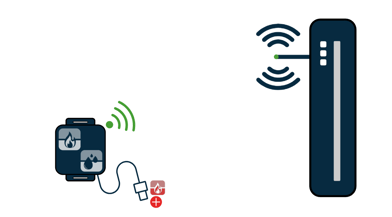
Moderne Sensorik erfasst kontinuierlich Betriebsdaten und analysiert diese mit künstlicher Intelligenz. Abweichungen vom Normalzustand – etwa Vibrationen, Temperaturänderungen oder akustische Signale – werden automatisch erkannt. So lassen sich beginnende Schäden an Motorlagern feststellen, bevor sie zu ernsthaften Problemen führen. Beispielsweise zeigt eine Untersuchung des Fraunhofer IPA, dass frühzeitige Anomalieerkennung die Lebensdauer von Maschinenkomponenten um bis zu 30 % verlängern kann.
Vorteile der Vibrationsüberwachung
-
Frühzeitige Erkennung von Verschleiß: Schäden an Motorlagern oder anderen beweglichen Teilen werden rechtzeitig erkannt.
-
Reduzierte Stillstandszeiten: Durch prädiktive Wartung lassen sich Ausfälle verhindern und die Produktivität um bis zu 25 % erhöhen.
-
Kosteneinsparung: Gezielte Wartung reduziert teure Notfallreparaturen und Produktionsausfälle – Unternehmen können bis zu 20 % ihrer Betriebskosten einsparen.
-
Effizientere Maschinenwartung: Wartungsintervalle können optimiert und unnötige Inspektionen um bis zu 30 % reduziert werden.
Warum ist Anomalieerkennung ein Gamechanger?-1.png?width=70&height=39&name=Website%20Tests-6%20(1)-1.png)
Viele Unternehmen setzen noch immer auf reaktive oder zeitbasierte Wartung, die oft ineffizient und kostspielig ist. Laut einer Studie von Deloitte liegt die durchschnittliche Stillstandzeit einer Maschine in der Industrie bei 800 Stunden pro Jahr, was je nach Branche Kosten von bis zu 50.000 Euro pro Stunde verursachen kann. Durch intelligente Sensorik und datenbasierte Analysen können Unternehmen ihre Maschinenlaufzeiten verlängern und Wartungskosten signifikant senken. Insbesondere in der Fertigungsindustrie, der Automobilbranche und der Energieerzeugung ist eine prädiktive Instandhaltung ein entscheidender Wettbewerbsvorteil.
Praxisbeispiele und Einsparpotenziale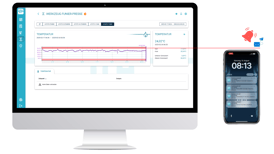
Ein großes Fertigungsunternehmen konnte durch den Einsatz von Vibrationssensoren und KI-gestützter Anomalieerkennung die Zahl der Notfallwartungen um 60 % senken. In einer anderen Fallstudie wurde nachgewiesen, dass durch Predictive Maintenance die Ersatzteilkosten um 15 % und die Energieeffizienz der Maschinen um bis zu 10 % verbessert werden konnten. Diese Werte zeigen, dass datenbasierte Wartungskonzepte ein enormes Potenzial zur Kostenoptimierung bieten.
Was bedeutet das nun? Kosten sparen durch intelligente Überwachung
Die Kombination aus Anomalieerkennung und Vibrationsüberwachung ermöglicht es Unternehmen, Schäden an Motorlagern frühzeitig zu identifizieren und Stillstandszeiten zu minimieren. Wer auf diese Technologie setzt, kann langfristig erhebliche Kosten sparen und die Effizienz der Maschinen steigern. Investitionen in prädiktive Wartung zahlen sich schnell aus und führen zu einem nachhaltigen Wettbewerbsvorteil. Experten prognostizieren, dass bis 2027 über 80 % der Industrieunternehmen Predictive Maintenance als Standardprozess implementiert haben werden.
Quellen und weiterführende Informationen
-
VDI-Bericht zur Zustandsüberwachung von Maschinen – Verband Deutscher Ingenieure (VDI) (https://www.vdi.de)
-
McKinsey & Company: Predictive Maintenance im Industrieumfeld – Bericht über Kostenersparnisse durch datenbasierte Wartung (https://www.mckinsey.com)
-
ISO 10816 – Internationale Norm zur Bewertung von Maschinenvibrationen – Standard für Vibrationsmessungen (https://www.iso.org)
-
COISS Sensorlösungen für Industrie & Holzverarbeiter– Praxisanwendung zur Anomalieerkennung und Vibrationsüberwachung (https://www.coiss.com)
-
Deloitte Industry 4.0 Report – Stillstandszeiten und Kostenanalysen (https://www2.deloitte.com)
-
World Economic Forum: Predictive Maintenance Trends – Zukunftsperspektiven und Marktprognosen (https://www.weforum.org)